Continuing with his Triumph Tiger 90 project, Tim Britton asks whether it’s really necessary to rip everything out of an engine and replace it wholesale before first utilising the careful measuring methods that could save a whole lot of unnecessary bother. Photos by Fiona Watson.
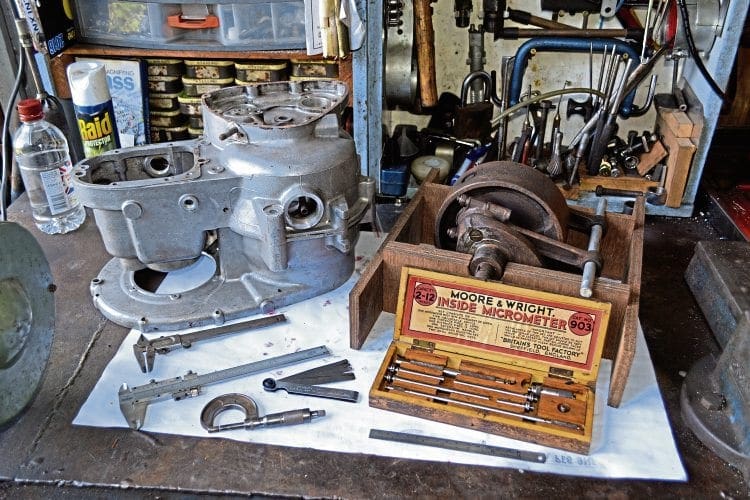
An engine such as the one in our Triumph project is an unknown quantity. Most of the bits inside are from 1961, and until it came apart there was no way of telling how it had been looked after… if it had been looked after at all.
We’re trying to make the text generic, but it just so happens that a 350cc unit twin Triumph was available. Okay, engineers look away now! It should be an obvious statement to say that bearings, shafts and bushes inside an engine all have a working clearance which is measured in thousands of an inch. If they didn’t, they’d seize or just wouldn’t go together.
Luckily, though, in the era covered by Old Bike Mart, manufacturers tended to list such figures in their handbooks, and a glance through three such books to hand – a Triumph twin instruction manual No. 4, a set of BSA service sheets for my B40 and my dad’s Matchless handbook –
shows all these figures in various lists, including the acceptable wear limits on parts such as big ends, little ends and crank journals where the main bearing is a bush, as with the early unit twin we’re using.
Typically there will be two figures, and as long as the component falls in between the two it should be safe to use.
Read more in the April issue of OBM – on sale now!